



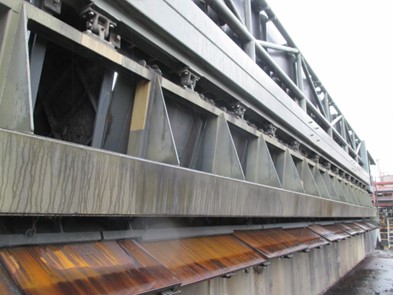
OVERVIEW: Engineers had tried and tested many different coatings with varied results for this Hot Coking Coal Quenching Structure.
Major structural steel repairs were carried out every two years due to the aggressive nature of this environment.

INDUSTRY
ENVIRONMENT
1,000°C Coking Coal transport wagon and moved to the quenching station, where 80°C recirculated water is used
SUBSTRATE
Mild steel substrate
CHALLENGE
Major structural steel repairs are carried out every two years due to the aggressive nature of this environment, the regular thermo cycling in service exceeds many coatings limitations. Oven temperature Coke is pushed in the Hot Car wagon where all of the coated surfaces are protected with sacrificial wear plates acting as heat shields where it is transported to the quenching area and an estimated 80 tonnes of recirculated water is dumped onto the Hot Coking Coal.
Engineers have tried and tested many different coatings with varied results. Main challenges are most of the work is carried out on site where abrasive blasting is not always possible due to the tight time schedule whilst other trades are working alongside the Chemcote Applications Team.
SOLUTION
We recommended Epo-chem™ RE 500P a high temperature resistant surface tolerant, Novolac Epoxy primer. Top coated with Epo-chem™ RW 500, glassflake filled, high temperature resistant Novolac Epoxy. The coating system provides excellent corrosion/erosion resistance against this environment.
SCOPE
Abrasive blasting to AS 1627.4 Class 3, 60µm profile on new sections in our workshop
All areas on site were mechanically cleaned using a scabbler, needle gun and bristle blaster to thoroughly remove all signs of corrosion. Application of RE 500P in one coat at 100µm nominal and application of RW 500 at 350µm Dry Film Thickness (DFT)
PRODUCTS
OUTCOME
Most linings were failing within a short period of time, between 2 & 8 weeks of service. An inspection of Chemco International’s high temperature coating systems after 2 weeks has indicated the lining is in excellent condition
RELATED CASE STUDIES
Fast Curing Abrasion Protection
Condition of surface before mechanical preparation RB 364 applied to spot abrasive blasted surfaces Pugmill externals Coating with InD Cote OVERVIEW: Chemcote’s specialist team
Split Case Salt Water Pump Refurbishment
Apply protection to all machined surfaces Application of 1st coat RB 364 Apply Ceram-Chem RP500 Ready to return to service for another 15+ years of
Composite Pipe Repair
Flange is barely attached Repairs commence Repairs using composite weave mat Coating complete OVERVIEW: A power station client required corrosion protection for a 30-plus