
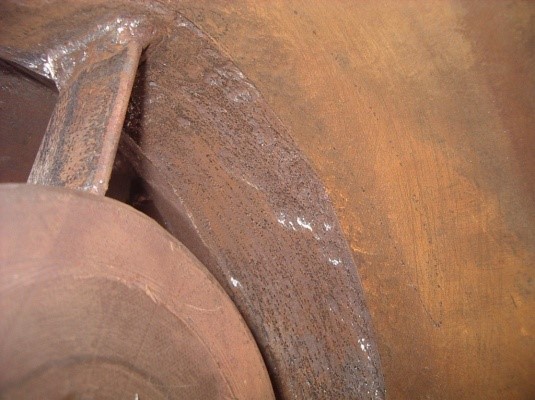


OVERVIEW: The refinery column pump for storm water and effluent required repairs and surface coating to protect from corrosion. Corrosion pitting and erosion was evident in the suction bell & adjoining column and the wear spacer ring/housing.
We recommended rebuilding the internal diameters affected by erosion corrosion to extend column pipe life and return pump to original efficiency

INDUSTRY
ENVIRONMENT
Storm Water, Effluent from Refinery
SUBSTRATE
Column pump
CHALLENGE
Column pump repairs were required and the surface coated to protect from corrosion. Corrosion pitting was evident in the suction bell & adjoining column. Erosion/corrosion was taking place in the wear spacer ring/housing.
SOLUTION
We recommended rebuilding the internal diameters affected by erosion corrosion to extend column pipe life and return pump to original efficiency
SCOPE
Abrasive blast to AS.1627.4 to class 2.5
Masking and protection of critical shaft tolerances
Pitting filled to allow smooth transition and prevent coating defects
Application of RA 532 internal & external
Pit-filled areas within impeller housing to ensure smooth finish
Application of RA 532 at a nominal thickness of 200 µm internal & external
Application of RP 500 internal
Application of Luxathane R ‘N35’ external
OUTCOME
The column pump repairs were timely, returning the unit to service within a week. A new replacement pump had a lead time of 16 weeks. The client was extremely happy thanks to the experienced Chemcote team and the exceptional qualities of the Chemco range.
RELATED CASE STUDIES
Blast Furnace Recovery Turbine Repairs
Set up of Containment Masking before Blasting Spool Condition before Coating Aerial view of Outlet Spool from Shutoff Valve Completed Outlet Spool Internals Application of
Long Term Protection Of ISOtainers
Newly fabricated tank internals Tank Internals Confined space entry Completed tanks for delivery to customer OVERVIEW: The asset owner approached us to provide protection
Floating Restaurant Structure Repairs Using Underwater Curing Epoxies
Condition before surface preparation Mechanical Preparation Primer Application Second Coat applied OVERVIEW: In the complete refurbishment of the underside of this floating structure, some